0
0
728
In this 3-part blog series, discover how Intel employees across design, manufacturing, and sales groups were involved in bringing to life a transformative technological advancement.
Launched early this September, Intel’s 11th Gen Intel® Core™ processor (formerly codenamed Tiger Lake) has taken the PC processor world by storm, heralding a new era of laptop performance. Optimizing power efficiency and running at significantly higher frequencies than its predecessors, it’s a technological leap so big that this is the largest performance gain yet within a process technology in the company’s history.
The product journey began three and half years ago and is the culmination of brilliance, perseverance, and teamwork that transcended global borders and time zones. It’s a product that Intel Malaysia is proud of, especially given its footprint and the number of key leadership roles Intel Malaysia it had in its development.
Below, read how AK Chong overcame unexpected challenges – including a global pandemic – to ensure the successful production and shipment of this game-changing product.
AK Chong, Factory Manager – SIMS
“When I think about the tiger, I think about something beautiful, fearless, and powerful. And it’s very well embodied by this processor.”
For Intel to ship a quality product, it must be tested. And the Systems Integration & Manufacturing Services (SIMS) factory in Kulim, led by AK, is the only Intel factory that builds test hardware that enables assembly tests manufacturers to test CPU units.
Given the significance and scale of the 11th Gen Intel Core processor, the factory started ramping up production in September last year, then the testers were shipped to the assembly test manufacturing plant in Chengdu. In March, just as production was peaking, the Covid-19 pandemic struck. As a result of the movement control order, only a skeleton crew could enter the site—and the factory could only operate at half capacity.
“When you’re ramping new testers, there’s a lot of debugging to do and we need engineers onsite to troubleshoot. But because we couldn’t have everyone in the factory at the same time, we had to plan carefully. And this included having engineers assisting those onsite over the phone from home. Prioritizing and de-prioritizing was necessary to make sure we didn’t miss a beat.”
Despite all the challenges that came with the restrictions, the team pulled through and still managed to fulfill the orders as originally expected, thus allowing the manufacturing site in Chengdu to successfully start production and ship the units.
“It was undeniably a difficult moment, but also one of my proudest. Many showed up even in the midst of all the fear, because they knew how important this was for the company. At the end of the day, it’s the people that make a difference, and our team did.”
Interested in learning more about what went into the design and sales of the 11th Gen Intel® Core™ processor? Read Part I and Part III of this blog series.
Want to be part of a creating world-changing technology that impacts the lives of everyone earth? Let’s do something wonderful together.
About the Author
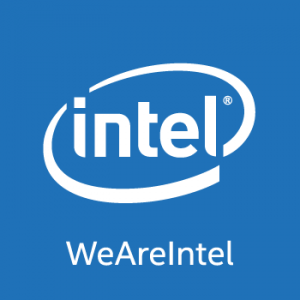
You must be a registered user to add a comment. If you've already registered, sign in. Otherwise, register and sign in.